Thomas Shea
Design Portfolio
Hot Wire Tool
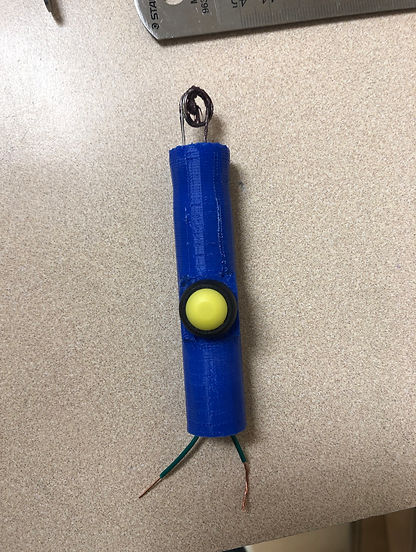
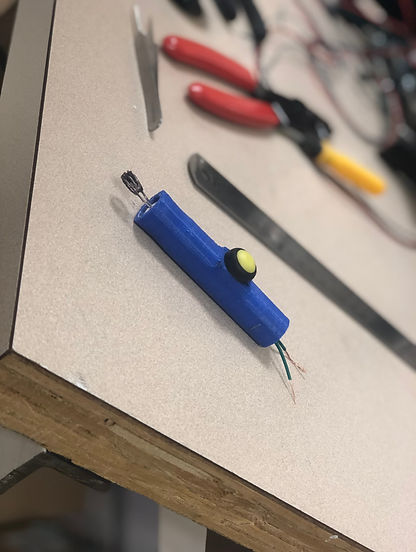
Within this project, a group of four of us worked together to produce a hand tool that uses heat dissipated across a nichrome wire to cut through something. In general, this project was designed to introduce us to different molding techniques for prototype creation, to practice determining what material(s) should be used to perform the necessary function, and to teach us some of the different ergonomic principles that go into certain design decisions.
​
More specifically, we were tasked with using six inches of 20 AWG nichrome wire, 12 inches of 20 AWG copper winter, and the electronic components in the button to produce a hot wire tool as shown in the above pictures. We were able to use a combination of molded, 3-D printed, and machined components in conjunction with the electronics. In the end we had to create this tool to allow users to shape, join, or apply finishing processes to thermoplastic materials.
​
The first part of the thought process was to determine what material to use to make the mold that would contain the wiring, and would go inside the larger part we were going to produce. Because the nichrome wire needed to have current through it, and the fact that the nichrome would get really hot, we had some constraints on what we could choose. We needed the mold material to have a high electrical resistance, as the current would not all go through the nichrome if the mold didn't. We needed the material to have a high melting temperature, so that it wouldn't melt when the tool was in use. Last, we needed the material to have low thermal conductivity, so that the users would have less of a burn risk when using the product. With all these constraints, the material options were limited down to either silicone, or clay. Our group elected to use clay for the mold, as it is a harder material, and would keep the wiring very secure once the mold was set.
​
When starting the design process, we had to decide how the user would hold the tool. Because the main application of the tool was said to be detailing thermoplastic materials, the ability to be precise was important for the tool. The tool was also not going to be very heavy, so we elected to go with a precision grip as opposed to a variation of the power grip. This gives the user the ability to be very careful with their work, and they will not have any struggle holding the tool. As shown in the above picture, the piece is not very large, so this was also conducive to a precision grip. We also decided to have the grip be slightly curved. This would make it even more comfortable for the user to hold, and also allowed us to have a little bit more protection for the user's hand from the heat of the cutting tool.
​
We were very happy with how our product came out, as the mold fit nicely and it looked how we were expecting it to. As shown in the sketches below, we were anticipating there to be more of a heat guard between the grip and the wire, but this did not fully go through to the final design.
​
This project was very effective in showing us how materials are chosen and why products may be shaped the way they are. We were able to discuss what we think would be potential materials for the mold and really consider what shape the final product would be. Being able to use play-doh to get an idea of what might be ergonomically satisfying was also very helpful in coming up with what should be the final design.
Sketches

Spencer Rogers' Sketch

Neil Doshi's Sketch

Thomas Shea's Sketch
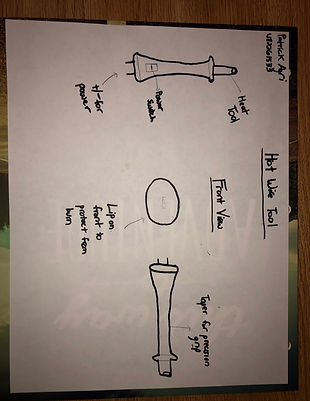